Batteries Receive a Second Life
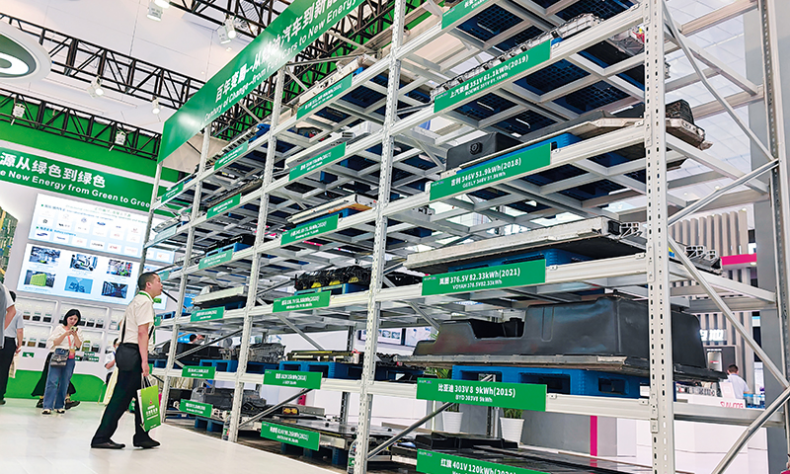
Chinese government has introduced several policies to encourage the development of the market for recycling and reusing traction batteries.
New stationary power storage cabinets have been set up beside the parking lots of the Green Eco Manufacture (GEM) Industrial Park in Wuhan, Hubei Province, to charge electric vehicles (EVs). Each cabinet contains five modules of used traction batteries that can be used for eight to 10 years before they need to be replaced.
These traction batteries are full of precious metals like lithium, cobalt and nickel. They’re what is often called the “power core” of EVs. Using these batteries again contributes to recycling resources and supports the growth of the EV industry. China recycled 825,000 tonnes of batteries in 2023, according to the Development Report of China New Energy Battery Recycling Industry (2024) published by the China Industrial Energy Conservation and Cleaner Production Association on 20 November last year.
An expanding market
The EV and battery industry in China is growing quickly. This means that recycling traction batteries has become a major priority. According to data compiled by Economic Daily, by the end of June 2024, the number of EVs in China had reached 24.72 million, accounting for 7.18 percent of all vehicles. This is an all-time record. However, a battery’s capacity decreases with the number of charge cycles. When the capacity gets below 80 percent, the batteries can’t meet the energy needs of the vehicles any more. China has been phasing out old traction batteries since 2018 because they only last for about eight years. These batteries need to be recycled and processed so that they can be used again. At the battery reuse plant in Wuhan’s GEM park, batteries that still have a relatively high capacity are sent to work tables. Robotic arms dismantle the modules and cells, which are then put back together to be used to power low-speed EVs, telecom base stations, power storage cabinets, and solar street lamps.
Batteries whose capacity has fallen sharply can also be reused. The extraction of precious metals for the production of new batteries reduces the demand for raw materials and the environmental impact of end-of-life batteries. Wan Xinming, deputy general manager of China Certification and Inspection Group, noted that recycling traction batteries helps to reduce carbon emissions.
The main companies in this sector in China are vehicle manufacturers, battery manufacturers and integrated recycling companies. One of the first companies to sign cooperation agreements on the reuse of traction batteries was the carmaker BYD, which has set up more than 40 battery collection points across China.
Another battery manufacturer CATL set up a 3.6 billion yuan ($491 million) joint venture with Guangdong Brunp Recycling Technology Co. in 2019 to expand its upstream battery business. Brunp Recycling was the first company to introduce the concept of integrated “upstream-downstream” recycling back in 2008, and it launched China’s first recycling system for used batteries. Today, it has 15 collection points in the country.
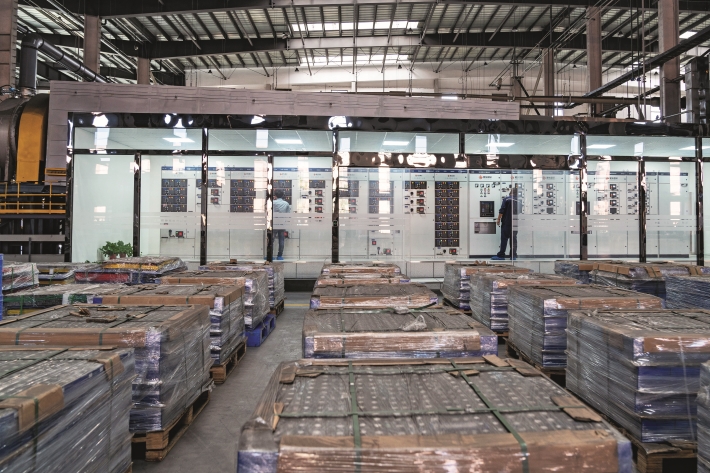
Li Li, vice president of the China Industrial Energy Conservation and Cleaner Production Association, said that by the end of October 2024, a total of 148 recycling companies had been selected and trained, and over 10,000 recycling service points had been set up across the country.
The amount of traction battery recycling capacity in China is increasing. According to the Traction Battery Reuse and Recycling Industry Report (2024), used battery recycling could reach 1.2 million tonnes by 2025, and 6 million tonnes by 2030.
Challenges and policy support
However, according to a survey by the Development Research Centre of the State Council, by the end of 2023, less than 25 percent of traction batteries in China had been recycled. In recent years, the government has introduced several policies to encourage the development of the market for recycling and reusing traction batteries.
In August 2024, the Ministry of Industry and Information Technology sought public opinions on the 2024 version of the Regulations for the Integrated Utilisation of Used EV Batteries. This new version has stricter requirements than the existing one released in 2019, particularly regarding site selection, capacity, product quality, production process, safety, environmental impact and technology.
One of the biggest problems with the reuse is making sure the batteries are of the same type. Sun Shan, deputy general manager of a company that specialises in replacing batteries, told China Media Group, “Reusing batteries involves converting them into new products. But there are so many different types of batteries that it’s really hard to make standards for them, and this is a big problem.”
To deal with this problem, the 2024 draft regulation requires car companies and battery makers to think about how to recycle batteries in a way that is good for the environment. This must be done right from the start of designing the products.
In addition, the traction battery recycling industry faces other obstacles, including low utilisation of collection points, persistent technical difficulties, and difficulties in enforcing standards. According to experts, it is essential that the government, businesses, and society work together to solve these problems through appropriate policies, technological research, and effective market regulation.
Li recommended speeding up the development of standards for the ecological design of used batteries, the assessment of their residual value and carbon calculation. He also called for greater cooperation between industry, academic institutions and researchers to solve these challenges, as well as intensifying international collaboration in the field of battery recycling.
With the volume of out-of-service batteries increasing rapidly, new players in the lithium battery value chain are accelerating their entry into the recycling market. However, significant technological gaps remain between companies, with some recovering more than 90 percent of lithium, while others recovering only 70 to 80 percent, according to the Development Report of China New Energy Battery Recycling Industry (2024). The report therefore recommends strengthening policy guidance and creating norms to effectively support industrial development, capacity allocation optimisation and integrated value chain development.