Shanghai Welcomes Intelligent Manufacturing
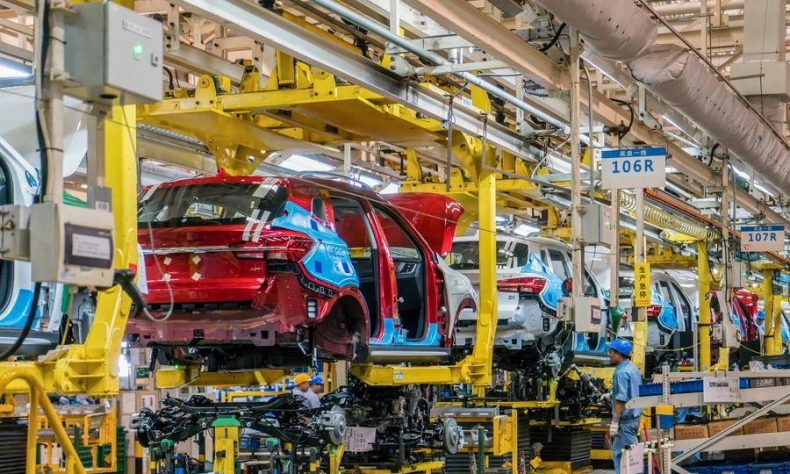
Fostering intelligent manufacturing bases is part of Shanghai’s effort to promote a green transition.
In recent years, Shanghai has begun implementing intelligent manufacturing projects. It has formulated plans for high-quality development, built high-standard smart factories, cultivated capable companies, and set up efficient public service platforms. As a result, it has gained an overall advantage with its high-end value chain, a complete industrial chain, a coordinated innovation chain, and a concentrated resource chain, which have made “Shanghai manufacturing” intelligent.
China Today took a close look at how conventional enterprises are realizing smart development and how industrial innovation is driven by technological innovation to develop new quality productive forces.
At SAIC Motor Passenger Vehicle Co.’s plant in Lingang in Shanghai, automated guided vehicles (AGVs) whiz past, transporting automotive parts to the production line where huge and nimble robotic arms perform some of the manufacturing procedures. This high-flexibility manufacturing base is the first of its kind in China to apply traditional and new-energy technologies throughout the manufacturing process.
Traditional giant hits a new track
Opened in 2008, the Lingang base, with an area of 1.2 million square kilometers, is one of SAIC Motor’s major manufacturing bases, producing vehicles and engines. It makes passenger vehicle products for the four major brands under SAIC Motor, namely IM Motors, Rising Auto, Roewe and MG, and is a landmark in this enterprise’s innovative transformation.
Guan Yizhong, general manager of SAIC Motor’s Public Relations Department, said in the past that SAIC Motor workers made the outer body panels manually, using hammers and iron mallets. Today, the base uses a digital operation system in the entire industrial chain, with collaboration between equipment and digital platforms
“Every 70 seconds a new car rolls off the assembly line in SAIC Motor’s Lingang base, or in other words, we make 43 cars each hour,” said Chen Peifeng, director of the Lingang vehicle factory of SAIC Motor.
In 2023, SAIC Motor sold a record 1.2 million units in overseas markets, up 18.8 percent year-on-year, the highest among domestic auto brands for the second consecutive year. This helped China surpass Japan in becoming the world’s largest car exporter. Its new-energy vehicle (NEV) sales were particularly impressive, with annual sales of 1.12 million units, a 4.6 percent increase from a year earlier, making it the second largest domestic NEV maker.
The Lingang base is a typical example of the transformation and upgrading of Shanghai’s traditional automotive industry. In response to the trend of smart, digitalized, and greener development, SAIC Motor is aiming to reach a higher level. According to data from the Shanghai Municipal Bureau of Statistics, Shanghai manufactured 1.29 million NEVs in 2023, up 35 percent from a year earlier, accounting for 13.4 percent of the national total.
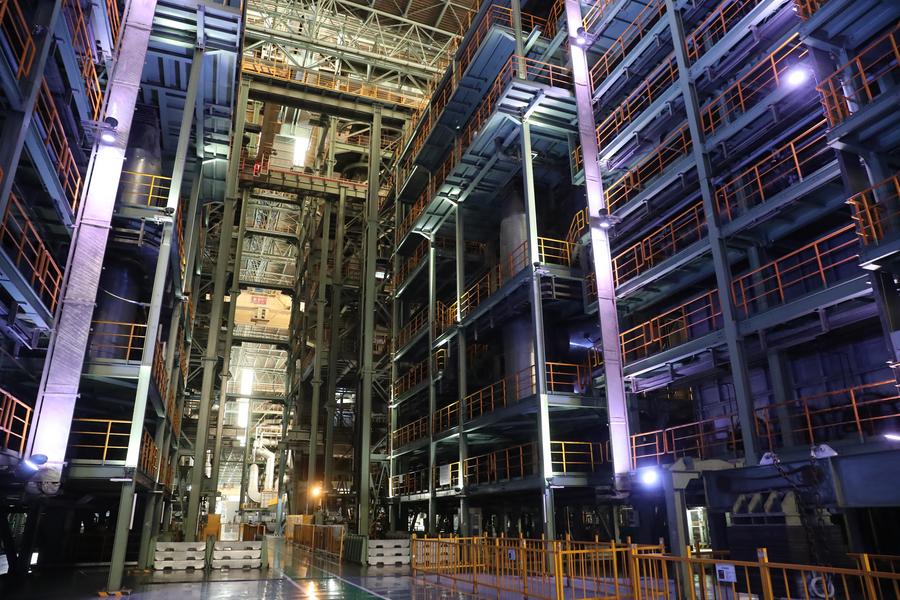
Green transition
Baoshan Iron & Steel (Baosteel) Baoshan base, 80 kilometers from the Lingang base, is another example of traditional Shanghai industries transforming into “intelligent manufacturing.”
Baosteel is the core enterprise of China Baowu Steel Group Corp., which is listed in Fortune‘s Global 500. Established in 1978, Baosteel led China’s steel industry onto the path of modernization. Today, it is promoting development through innovation. “We pursue higher-end, smarter and greener development, seeking to optimize and upgrade the entire industrial chain,” Baosteel’s General Manager Wu Xiaodi said.
In a smart workshop for automotive panels at Baosteel’s cold coiling factory, overhead cranes move up and down and unload steel coils smoothly without any driver or ground operator. The entire working area is almost dark, earning it the name “Lights-out Factory.”
The “Lights-out Factory” is a smart factory. Baosteel’s cold coiling area employs the highest number of robots on the manufacturing line in China. In addition to the unmanned cranes, other automated operations include automated robot spraying, intelligent inspections, automatic slag removal, and automatic unbundling. It is the first unmanned smart factory in China’s steel industry where several operations can be completed automatically, significantly improving workplace safety and operational efficiency.
The iron and steel industry is a major energy consumer and a significant emitter of carbon dioxide, so its green and low-carbon transformation is crucial to China’s sustainable development. Baosteel has a 30-year-old “Sentinel Zoo”, housing sika deer, pigeons, and peacocks. “Sentinel” is an apt name for it because it shares the responsibility of monitoring Baosteel’s environment. “These animals are sensitive to environmental conditions. Some pollutants cannot be detected by instruments but some animals act like environmental monitors, providing real-time feedback on the factory’s ecological conditions,” Li Jungong, engineer and director of zoo management, told China Today.
Liu Shijun, deputy general manager of the operation center at Baosteel, said the company regards China’s “dual carbon” goals as its own goal. It has established demonstration production lines of zero-carbon iron and steel and made breakthroughs in key low-carbon metallurgy technology. In 2022, Baosteel announced it would achieve the technical capability to reduce carbon emissions by 30 percent by 2025, realize the 30 percent reduction by 2035, and become carbon neutral by 2050. Liu pointed out that over the past six years, Baosteel has achieved energy savings equivalent to 1.2 million tons of standard coal, or reducing three million tons of carbon dioxide emissions each year.
Ge Dongbo, chief engineer of Shanghai Municipal Commission of Economy and Informatization, said Shanghai has promoted the transformation and upgrading of its manufacturing industry with industrial innovation as its core driver to create a new development impetus. Besides, it is promoting digital transformation in its manufacturing sector by developing industrial networks and intelligent factories.
Shanghai, a pioneer in establishing an intelligent factory hub, has fostered three national intelligent factory models, 19 state-level demonstration intelligent factories, 111 state-level excellent intelligent manufacturing scenarios, and 177 municipal-level intelligent factories. An intelligent factory can increase productivity by 50 percent while decreasing operational costs by 30 percent and energy consumption per unit of added value by 13.8 percent. All this is helpful in developing new quality productive forces.